Key application areas for DUPLEX F2 printer
for R&D labs, Automotive
and Technical Sports
Functional prototyping is one of the key areas where 3D printing has been able to add great value to the innovation processes of several industries.
However, the creation of ready-to-use, real-size functional prototypes of long and complex shapes was not possible without the use of extensive support structures requiring human labor intensive post processing.
for Medical sector, Design
and Film Production Studios
Additive manufacturing increasingly supports various areas of industry in the production of high-added-value, unique geometries and primarily small-series products.
Although medical use due to its patient-specific needs has an outstanding potential for the wider implementation of 3D printing, the technology’s slowness, high costs, and the need of complicated post-process work significantly limits its use in medical application.
for Machinery and
Manufacturing industries
Fast response time on the factory or assembly floor is crucial in any manufacturing process.
However, creating lasting fixtures and accurate jigs is mostly outsourced to reduce in-house complexities and the need for human labor-intensive post processing.
This often creates loss of assembly line utilization, reducing overall factory production efficiency.
for
Manufacturers
Conventional production processes such as CNC milling are generally costly and time consuming and they require a large amount of preparation time, therefore the industry is turning to AM to produce printed tools and fabrication molds, as 3D printing processes offer a great deal of freedom by liberating the design process of the conventional technologies’ restrictions.
The new generation of FDM printers
If you can print in two-directions, why would you print in only one?
- Real-size functional prototypes of complex shapes
- Prints ready to use molds
- Up to 15 times faster total production process
- Environmentally friendly, due to low support material & energy need
- Applicable for PLA, PET, ABS, ASA, PP, PA & CF/GF xreinforced PA
Technical specs
Build Volume ∅ 400 mm x 1000 mm
Machine Dimensions 912 mm x 1176 mm x 2654 mm
Custom build plate up to 130 C
Heated Chamber up to 80 C
Z layer resolution 50 – 600 micron
Web-based remote software control
Fully automated thermal control system
Automated mid-section operation for high quality two-way printing
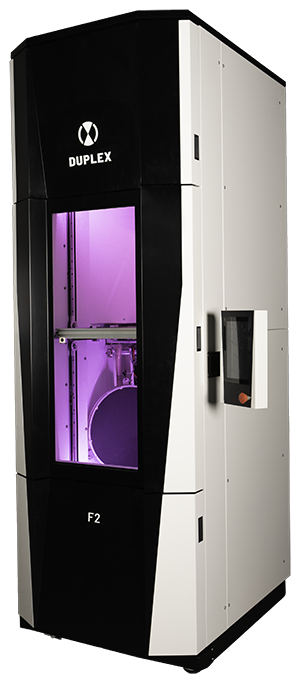