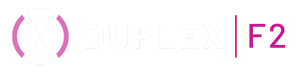
The new generation of FDM printers!
DUPLEX F2 is developed based on the patented MAP™ technology, enabling the printing of an object from two different directions at the same time.
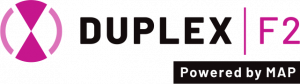
The new DUPLEX F2 printer is designed for heavy, industrial application, built from quality parts and assembled with precision to assure the long lasting quality and reliability this new technology truly deserves. Thanks to the multi-directional part growing, the DUPLEX F2 gives up to 15-times faster total production process than other FDM printers due to the combination of its unique features
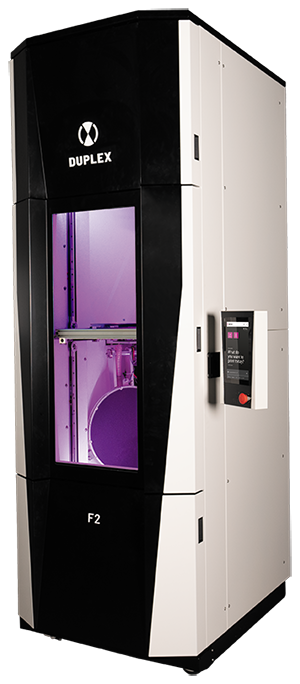
Benefits

Less to no supports
Support structures are unnecessary for most of shapes

Fully automated
Autonomous operation of multiple print directions

Wide range of thermoplastics
Applicable for PLA, PET, ABS, ASA, PP, PA & CF/GF reinforced PA

Designed for elongated, complex shapes
Build chamber designed to fit most parts in our target industries

Smart processing
Proprietary slicing software to handle two-way printing

High speed printing
Optimized for BASF filaments including PLA PRO1
Key Innovations
- MAP™ technology: parallel, simultaneous printing from multiple directions of the same object
- AutoPlane System (APS): APS automatically removes the base plate, allowing the bottom extruder to access the object for parallel printing from top and bottom at the same time
- Proprietary DUPLEX software to handle unique MAP™ slicing needs: the DUPLEX processing software is a powerful tool for 2-way part slicing
- Auto check system: advanced part error recognition algorithm
- Mesh auto calibration: mesh plate calibration for perfect part orientation
- Remote support: diagnostics and printing tech support carried out remotely by our DUPLEX specialists
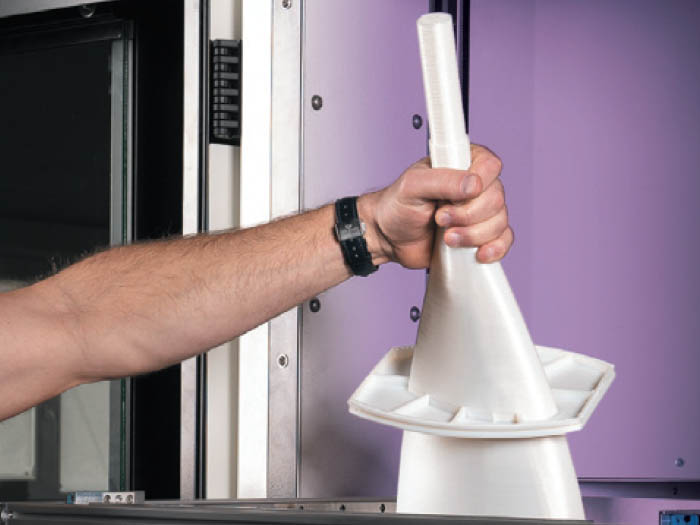
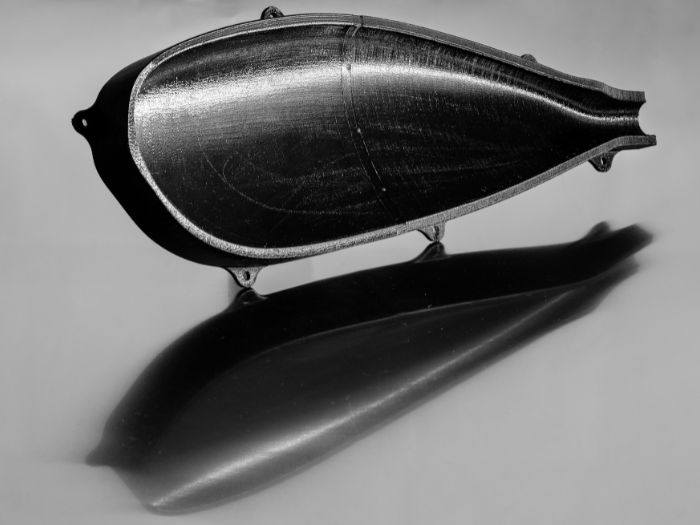
Printed without any support
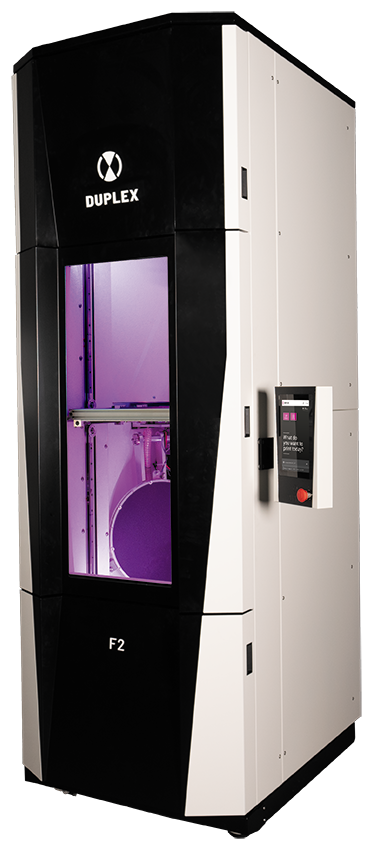
Technical Specs
Built Volume
∅ 400 mm x 1000 mm
Machine Dimensions
912 mm x 1176 mm x 2654 mm
Custom build plate
up to 180 C
Heated Chamber
up to 80 C
Z layer resolution
50 – 600 micron
Web-based remote software control
Fully automated thermal control system
Automated mid-section operation for high quality two-way printing
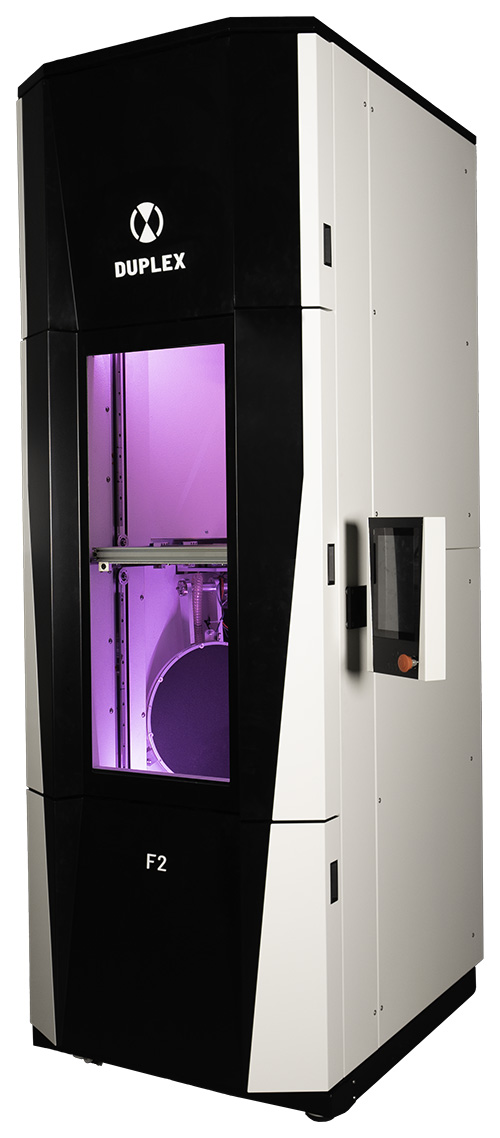
Technical Specs
Built Volume
Diameter – 400mm
Height – 1000mm
Machine Dimensions
Width – 880mm
Debth – 106mm
Height – 2400mm
Features
PEI covered print plate up to 130 C
Heated Chamber up to 80 C
Z layer resolution 50 – 600 micron
Remote software control
Fully automated system
Fully automated sytem
Same mechanical properties as one-directional printing
Independent testing carried out by the Polymer Department of the Budapest University of Technology
For independent mesurements of the F2’s printered parts, the company has contacted the Faculty of Polymer Technology at the Budapest University os Technology and Economics. Their measurements on a kayak paddle part are published on this page.
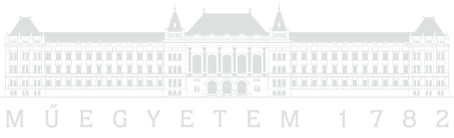
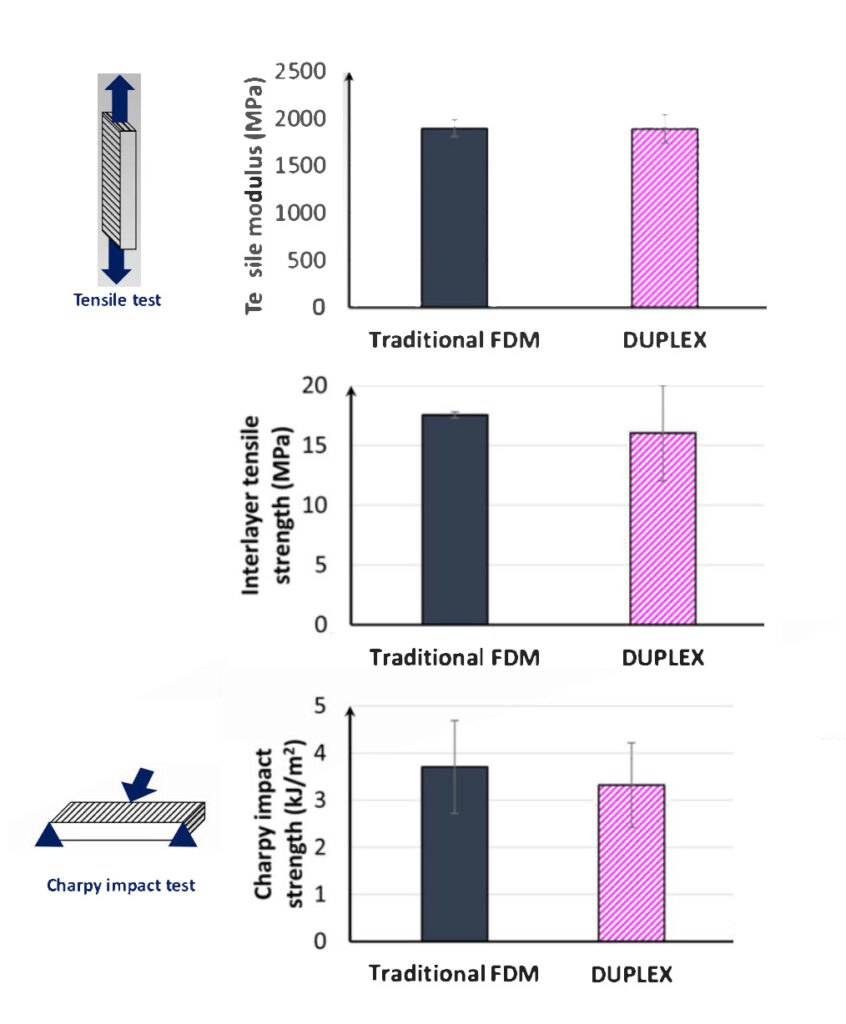
Test Results
Tensile test results showed that there is no significant difference between conventional FDM 3D printing and two-way building of parts, with the latter causing only a slight reduction in the interlayer strength and the modulus remains unchanged.
Charpy impact tests also showed a slight reduction in average impact strength, although the difference is not considered significant due to overlapping scatter fields.