Easily create high-performance composite molds
Ready to use Molds and Patterns for Manufacturers
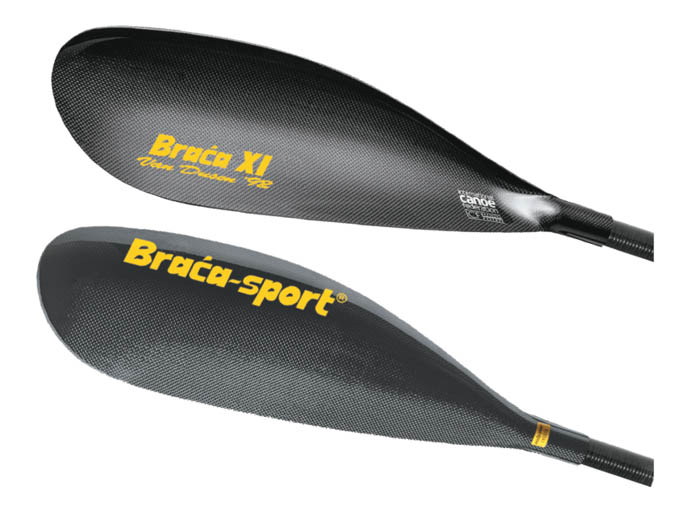
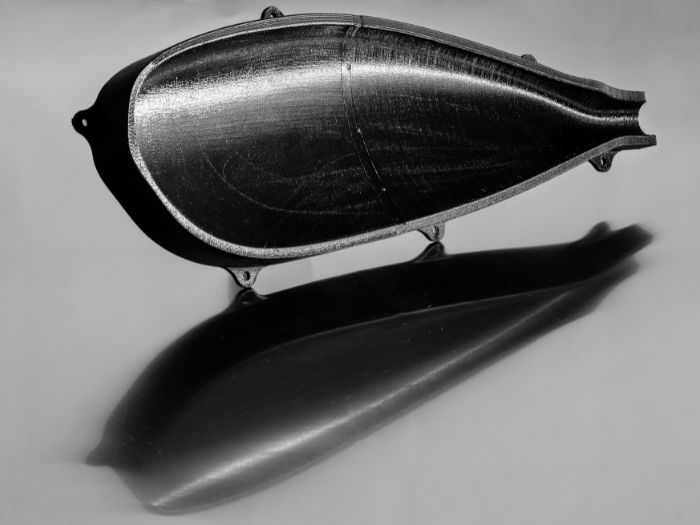
The 3D printing processes offer a great deal of freedom
Conventional production processes such as CNC milling are generally costly and time consuming and they require a large amount of preparation time, therefore the industry is turning to AM to produce printed tools and fabrication molds, as 3D printing processes offer a great deal of freedom by liberating the design process of the conventional technologies’ restrictions.
DUPLEX F2 takes 3D printing of molds a step further: it does not only make FDM considerably faster but – due to two-directional printing – also eliminates the need for most of the support structures, minimizing the need for post processing, making the overall 3D production process of complex shaped, high performance composite laminate molds up to 15 times more productive than any other FDM printer.
Rapid Prototyping for R&D labs, Automotive and Technical Sports
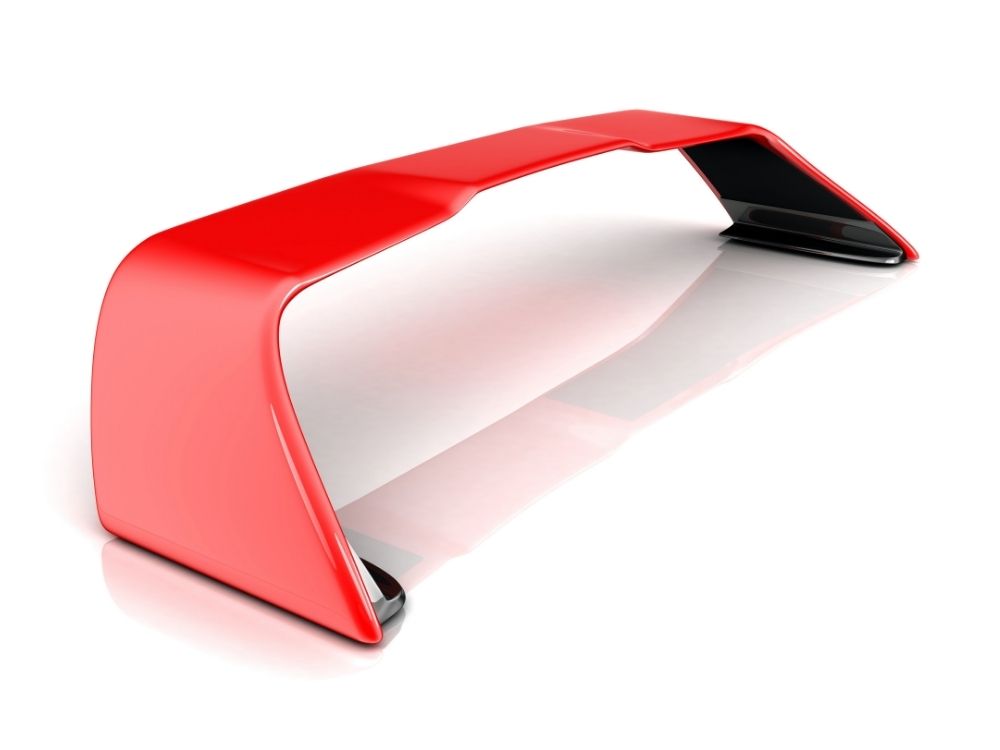
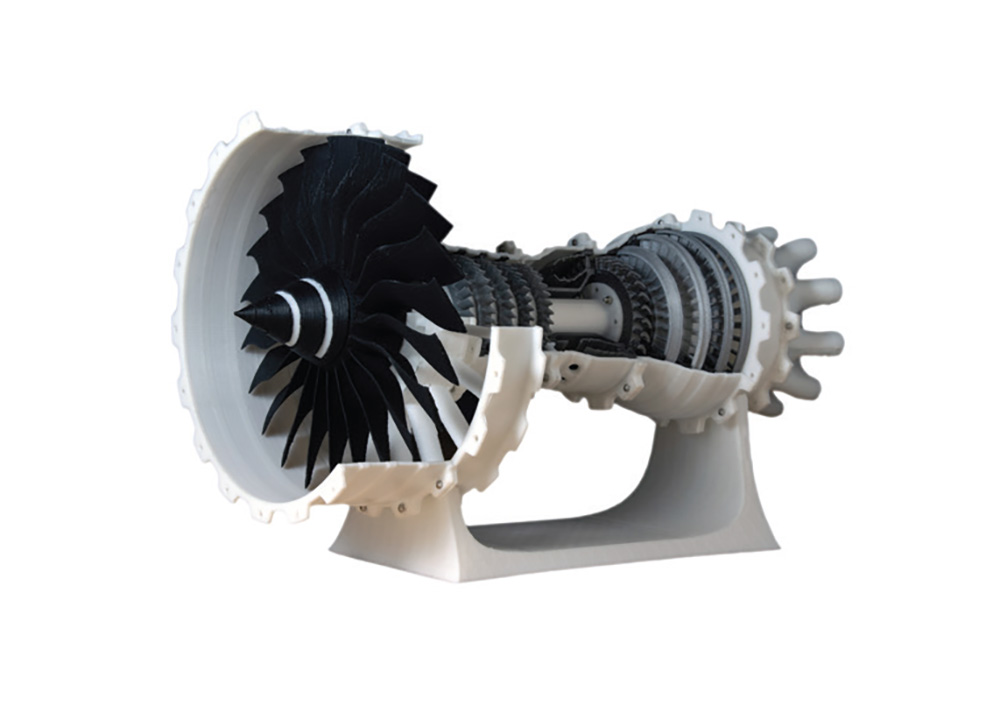
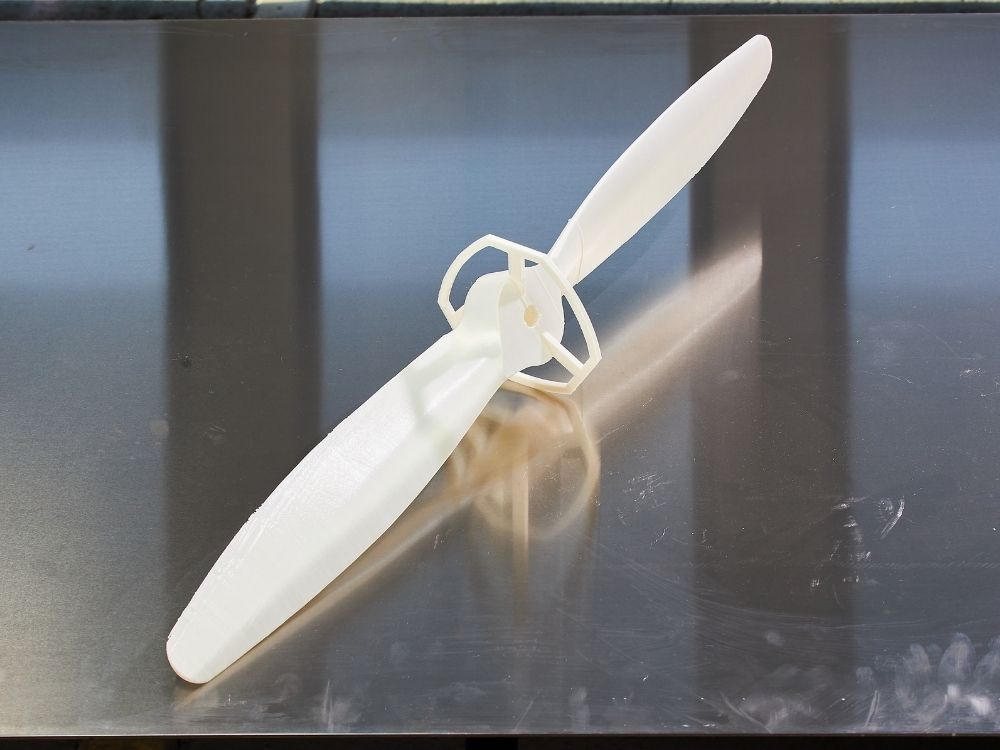
Functional prototyping is one of the key areas
where 3D printing has been able to add great value to the innovation processes of several industries.
However, the creation of ready-to-use, real-size functional prototypes of long and complex shapes was not possible without the use of extensive support structures requiring human labor intensive post processing.
The MAP™ powered two-directional printing – building the object from its mid-section – allows DUPLEX F2 to efficiently print elongated and curved shaped functional prototypes the same day it comes off the desk of the designers.
Thanks to its effective heated chamber, DUPLEX F2 can print engineering plastics, such as PC, and even carbon- and glass reinforced PA materials, producing not only ready-to-use functional prototypes, but even end-parts.