Du modèle 3D au test dans l'eau en 2 jours.
Brača-Sport a utilisé les imprimantes tridimensionnelles industrielles F2 de DUPLEX pour faire passer leur cycle de prototypage de 90 jours à tout juste 2 jours ; elles ont aussi permis de réduire leurs coûts de fabrication des moules.
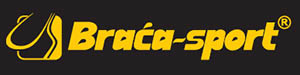
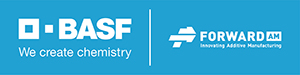
Résumé
Réduction du temps de développement
de 90 jours à 2 jours
Temps d'impression d'une paire de pagaies
15 heures
Temps d'impression de paires de moules
22 heures
Réduction des coûts de main-d'œuvre et de moules
78%
« Nous souhaitons proposer les pagaies les plus efficaces en terme d’énergie pour propulser plus rapidement les athlètes ; c’est la raison pour laquelle nous avons autant de modèles différents. Avec DUPLEX, nous réduisons la durée du processus de développement et nous avons enfin la possibilité de tester quelques modèles originaux et un peu fous. »
András Trebitsch – CEO, Brača-Sport
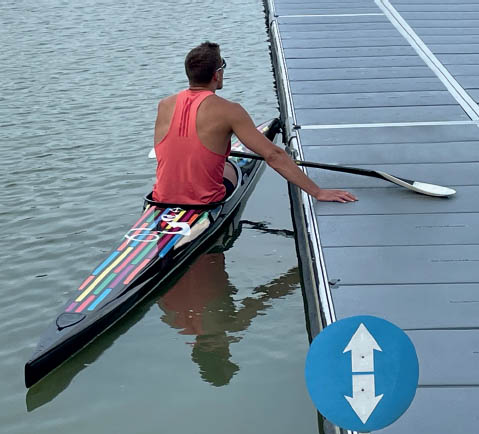
La mission de Brača-Sport est de concevoir, développer et produire les pagaies high-tech les plus performantes pour les athlètes olympiques.
Au cours des 30 dernières années, ils ont collaboré avec des athlètes et entraîneurs professionnels de kayak et de canoë les plus performants au monde.
Brača-Sport timeline
1991 –
1994 –
2000 –
2020 –
Une précision d'impression irréprochable
L’échantillon a été numérisé dans les laboratoires de la Faculté de technologie des polymères à l’aide d’un système de mesure optique 3D GOM ATOS Core 5M.
Le nuage de points ainsi obtenu a ensuite été ajusté au modèle CAO original de la pièce mesurée. C’est sur cette base que l’impression a été réalisée à l’aide de l’imprimante F2 de DUPLEX.


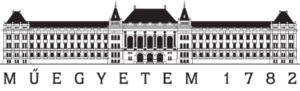
Des tranches ont été créées sur l’échantillon numérisé tous les 10 mm dans la direction Z.
La position du centre de gravité a été calculée dans les plans X et Y, aussi bien pour les données CAO d’origine que pour le modèle scanné en 3D.
Les périmètres de chacune des coupes transversales ont également été calculés.
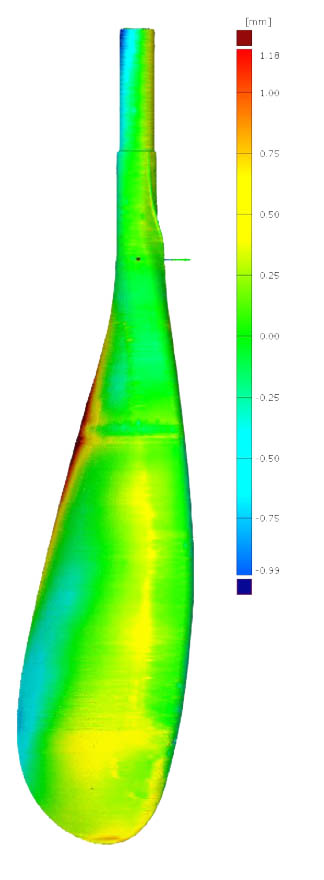
De 3 mois à 2 jours avec DUPLEX
„Ce que nous cherchons à obtenir avec le nouveau design de notre dernière pagaie – une version modifiée de notre pagaie Brača XI – c’est que l’athlète dépense le moins d’énergie possible et que toute l’énergie soit transformée en mouvement vers l’avant.”
– Ajoute Tamás Ledeczi, directeur technique de Brača-Sport.
„La technologie DUPLEX nous permet d’imprimer une paire entière de pagaies de taille normale en moins de 24 heures. Après une journée de post-traitement, la conception peut être testée en conditions réelles. Avec notre technologie précédente, cela aurait pris 3 mois.”
Une paire de pagaies Brača XI modifiée a été imprimée sur DUPLEX F2, à l’aide du matériau BASF Forward AM Ultrafuse®, en 15 heures. L’impression n’a pas nécessité de support supplémentaire en dehors de la partie mid-plate nécessaire à la suspension de l’objet pour une impression bidirectionnelle. Après le retrait de la partie médiane de la plaque, aucun post-traitement supplémentaire n’a été nécessaire.
Après avoir fixé les pales imprimées sur les manches, le prototype fonctionnel de pagaie a été testé dans l’eau, en situation réelle, afin d’évaluer ses performances. Sur la base de cette expérience, le modèle a été légèrement modifié pour poursuivre le processus de développement itératif.
„Les sports techniques exigent beaucoup d’innovation. Souvent, ces innovations passent par un processus itératif, qui nécessite beaucoup de prototypage. Il faut voir comment cela fonctionne, et il faut l’utiliser dans la vie réelle.”
– explique David Aniot, directeur du développement commercial et du marketing chez DUPLEX.
La fabrication de moules : une nécessité coûteuse
Le cœur de la technologie de Brača est un système unique de moulage des pales qui évite la pénétration de l’eau et apporte une résistance et une rigidité supplémentaires à la pagaie. Ce système offre une durabilité maximale et une protection exceptionnelle contre les chocs par rapport aux pales composites conventionnelles qui ont dont le noyau de mousse est exposé sur le bord ouvert et qui sont vulnérables aux dommages et à l’inévitable pénétration de l’eau.
„Le plus grand défi pour nous est que les coûts de développement et de fabrication des moules représentent une part très importante des coûts totaux. Jusqu’à présent, tout a été fait à la main.”
– explique András Trebitsch, PDG de Brača-Sport, à propos d’un des challenges majeurs.
„Travailler avec DUPLEX est une grande opportunité. Ils sont très créatifs et serviables et je vois un avenir très positif en travaillant avec leur technologie en interne.”
La fabrication de moules est depuis longtemps une difficulté à surmonter. Les moules en fibre de carbone et autres moules de stratification sont généralement soit fraisés par commande numérique à partir d’un bloc de matériau solide, soit composés à partir d’une pièce prototype à l’aide d’un processus manuel en plusieurs étapes. Ces deux méthodes prennent beaucoup de temps et la main-d’œuvre représente un coût important, car ces processus nécessitent beaucoup de manipulations de la part d’opérateurs qualifiés.
DUPLEX F2 peut imprimer des géométries complexes même à partir de matériaux très robustes comme le PA résistant à la chaleur ou le PA renforcé au carbone. Grâce à cela, nous pouvons construire très rapidement des moules et des modèles de grande taille.
“L’utilisation de matériaux BASF a été d’une grande aide car elle a permis d’obtenir des résultats de haute qualité qui peuvent être imprimés plus rapidement qu’avec d’autres matériaux.”
– conclut M. Aniot.